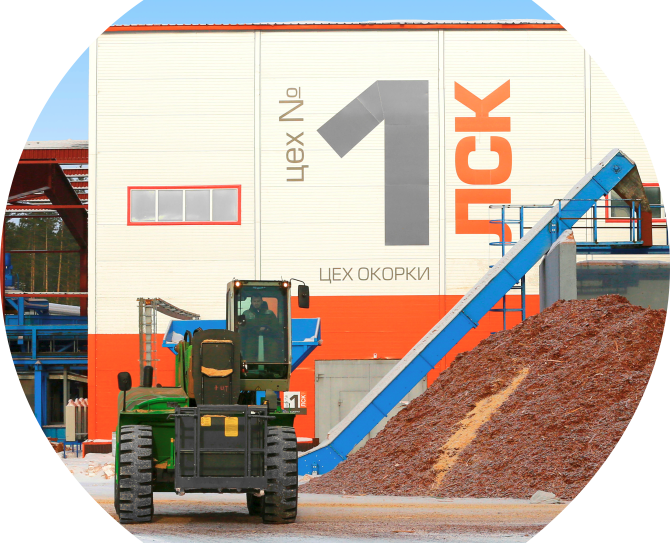
WASTE-FREE PRODUCTION SYSTEM
Kraslesinvest plant implements a waste-free production system. Bark, sawdust, and chipped wood, remaining after wood processing, are shredded by the Vecoplan grinder (Germany) up to the required grade and used as combustible for the boiler station built by Polytechnik company, Austria. Capacity of the boiler station is 20 MW – two boilers of 10 MW each. It provides enough heat for the chamber driers. Besides, part of the energy is used to heat the facility and boardinghouse. The in-house boiler station fired by biofuel allows the company to save a lot of expenditures for heating.
The company has begun construction of the pellet plant to ensure complete processing of chipped wood.
Project Goal and Tasks. Effects of project execution: Creation of modern biofuel production. Sawmill plant materials recovery in the volume of 830 thous. m3 per year. Rise of the interest in alternative and renewable energy sources taking into account strict ecological safety requirements.
Raw wood is the main technological resource for production of the wood fuel pellets based on the planned performance of 105 kilo ton: sawmill plant waste materials – chipped wood and sawdust.
The pellets are produced without any chemical additives that ensures ecological cleanness of the fuel. In other words, the pellets are firewood in a convenient form for transportation, storage and use. The bonding material is lignin –the natural wood component that bonds the particles at a certain temperature. The pellets produce 20 times less cinder then coals.